Table of Contents
Coated fabrics are an essential component in industries ranging from construction and automotive to manufacturing and medical applications. These fabrics are enhanced with a variety of coatings that impart valuable properties such as waterproofing, UV resistance, temperature resilience, and chemical resistance. Whether it’s for automotive seat covers, tarpaulins, protective clothing, or roofing materials, understanding the differences between types of coated fabrics is crucial for professionals in these sectors. Each type of coating offers unique advantages, making it important for businesses to select the right fabric for specific needs.
This article will break down the different types of coated fabrics, how they are applied, and provide real-world examples to help you make informed decisions for your business.
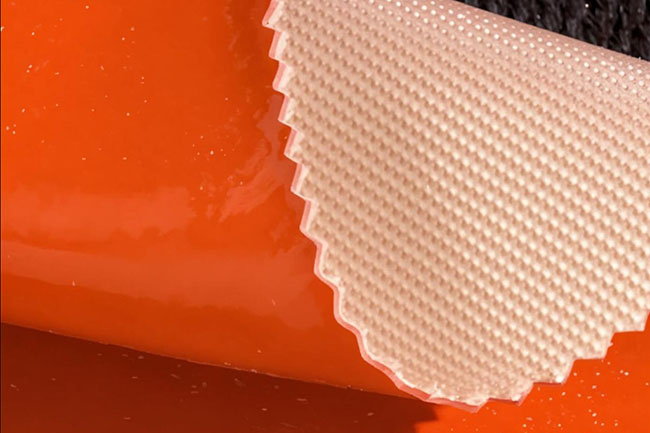
What Are Coated Fabrics?
Coated fabrics are textiles that have been treated with a layer of coating material such as PVC, polyurethane (PU), silicone, Teflon, PTFE, or acrylic. These coatings significantly enhance the fabric's properties, making them ideal for a wide range of industrial and commercial applications. By bonding these coatings to the fabric through various methods such as dipping, spraying, or lamination, manufacturers can create fabrics that are more durable, weather-resistant, and flexible. The result is a fabric that is more suited to withstand demanding environmental conditions and physical stresses.
Types of Coated Fabrics
Each type of coated fabric offers distinct advantages. Below is a detailed breakdown of some of the most commonly used coating materials, along with their properties, benefits, and typical applications.
1. Silicone-Coated Fabrics
Silicone-coated fabrics are known for their outstanding heat resistance and flexibility, making them ideal for high-temperature environments.
- Key Properties: High-temperature resistance (up to 500°F), excellent UV resistance, flexibility, chemical resistance.
- Benefits: Durable under extreme conditions, excellent for long-term outdoor exposure, flexible even in cold temperatures.
- Typical Applications: Aerospace (e.g., heat shields), automotive (e.g., engine covers), food processing (e.g., oven curtains).
2. Polyurethane-Coated Fabrics
Polyurethane coatings are popular for their abrasion resistance, flexibility, and cost-effectiveness, making them a go-to for industries that require a balance of durability and comfort.
- Key Properties: Moderate heat resistance (up to 180°F), water resistance, abrasion resistance, breathable.
- Benefits: Lightweight, flexible, breathable, and affordable.
- Typical Applications: Automotive (e.g., seat covers), fashion (e.g., raincoats), sportswear (e.g., waterproof jackets).
3. PVC-Coated Fabrics
PVC coatings are one of the most cost-effective options available and are widely used for applications that require waterproofing and UV stability.
- Key Properties: Excellent waterproofing, UV resistance, electrical insulation, chemical resistance.
- Benefits: Affordable, highly durable, waterproof, and highly resistant to weathering.
- Typical Applications: Construction (e.g., tarps, tents), outdoor furniture, industrial covers.
4. Teflon-Coated Fabrics
Teflon-coated fabrics are renowned for their non-stick properties and chemical resistance, making them ideal for food-related and chemical-processing industries.
- Key Properties: Chemical resistance, non-stick surface, high-temperature tolerance (up to 500°F).
- Benefits: Excellent for food processing and chemical environments, easy to clean and maintain.
- Typical Applications: Food processing, medical textiles, chemical industries.
5. PTFE-Coated Fabrics
PTFE (Polytetrafluoroethylene) is a more advanced version of Teflon and is known for its extreme durability and chemical resistance.
- Key Properties: High temperature and chemical resistance, low friction, non-stick.
- Benefits: Extremely durable, resistant to high temperatures, long lifespan even in harsh conditions.
- Typical Applications: Industrial filtration, pharmaceuticals, food handling.
6. Acrylic-Coated Fabrics
Acrylic-coated fabrics are often chosen for their UV resistance and lightweight properties, making them a popular choice for outdoor and weather-exposed applications.
- Key Properties: UV resistance, water resistance, color fastness.
- Benefits: Lightweight, affordable, good for outdoor environments, weather-resistant.
- Typical Applications: Outdoor furniture, awnings, marine upholstery.
Comparison of Coated Fabrics
Property | Silicone | Polyurethane | PVC | Teflon/PTFE | Acrylic |
---|---|---|---|---|---|
Temperature Resistance | ✔ (up to 500°F) | ✘ (up to 180°F) | ✘ (up to 180°F) | ✔ (up to 500°F) | ✘ (up to 180°F) |
Chemical Resistance | ✔ | ✔ | ✔ | ✔ | ✘ |
UV Stability | ✔ | ✔ | ✔ | ✔ | ✔ |
Abrasion Resistance | ✘ | ✔ | ✔ | ✔ | ✔ |
Waterproofing | ✔ | ✔ | ✔ | ✔ | ✔ |
Cost-Effectiveness | ✘ | ✔ | ✔ | ✘ | ✔ |
Breathability | ✘ | ✔ | ✘ | ✘ | ✔ |
Applications | Aerospace, automotive, food processing | Fashion, automotive, medical | Industrial covers, tents, tarpaulins | Food processing, medical | Outdoor furniture, awnings |
Technical Breakdown: How Coating Is Applied
The coating application process significantly influences the final properties of the fabric, including its flexibility, chemical resistance, waterproofing, and durability. Here are the most common methods used for coating fabrics:
1. Dip Coating
In dip coating, the fabric is immersed in a liquid coating solution, which is then cured to create a durable, uniform layer. This method is excellent for waterproof fabrics but may result in less flexibility in some cases.
- Advantages: Provides a uniform coating, excellent for waterproofing and heavy-duty applications.
- Limitations: May reduce fabric flexibility and increase weight.
- Best For: Industrial tarps, outdoor covers, waterproof textiles.
2. Spray Coating
In spray coating, a fine mist of coating material is applied to the fabric’s surface. This process is suitable for lighter coatings and decorative applications.
- Advantages: Smooth finish, even coating, ideal for thin coatings.
- Limitations: Requires multiple layers for durability, may be less effective for heavy-duty uses.
- Best For: Fashion textiles, light-duty covers, automotive upholstery.
3. Lamination
Lamination involves bonding a thin layer of coating material onto the fabric using heat and pressure. This process results in a highly durable fabric that is ideal for high-performance applications.
- Advantages: Excellent for waterproofing and weatherproofing.
- Limitations: More expensive than dip or spray coating.
- Best For: Medical textiles, protective gear, outdoor fabrics.
Decision-Making Solutions: Choosing the Right Coated Fabric
To help professionals choose the best coated fabric for their needs, we’ve created the following decision matrix:
Factor | Silicone | Polyurethane | PVC | Teflon/PTFE | Acrylic |
---|---|---|---|---|---|
High-Temperature Resistance | ✔ | ✘ | ✘ | ✔ | ✘ |
Chemical Resistance | ✔ | ✔ | ✔ | ✔ | ✘ |
UV Stability | ✔ | ✔ | ✔ | ✔ | ✔ |
Abrasion Resistance | ✘ | ✔ | ✔ | ✔ | ✔ |
Waterproofing | ✔ | ✔ | ✔ | ✔ | ✔ |
Cost-Effectiveness | ✘ | ✔ | ✔ | ✘ | ✔ |
Breathability | ✘ | ✔ | ✘ | ✘ | ✔ |
By analyzing the requirements of your project, you can use the matrix to make an informed decision on which coating to select.
Case Studies and Real-World Applications
- Automotive Industry: Polyurethane-coated fabrics are widely used in automotive seat covers due to their balance of abrasion resistance and flexibility.
- Construction: PVC-coated fabrics are commonly used for tarps, industrial tents, and temporary shelters due to their waterproofing and UV resistance.
- Aerospace: Silicone-coated fabrics are used in heat shields and protective coverings due to their high-temperature resistance.
Conclusion
Choosing the right coated fabric is essential for ensuring the durability and performance of products in various industrial sectors. By understanding the properties of silicone, polyurethane, PVC, Teflon, PTFE, and acrylic coatings, professionals can select the optimal fabric for their needs. Whether it’s for high-temperature environments, chemical processing, or waterproofing, the correct coating will enhance product performance and longevity.
If you need help selecting the right fabric for your project, don’t hesitate to consult with experts or explore a variety of coated fabrics tailored to your specific application.