Table of Contents
Para-aramid and meta-aramid fabrics are both high-performance synthetic fibers known for their durability, heat resistance, and mechanical strength. Widely used in industrial applications, these fabrics are coated with silicone rubber to enhance their properties, making them suitable for a range of demanding environments. This article explores what para-aramid and meta-aramid fibers are, their unique advantages, and how to choose the right one for your needs—especially when enhanced with silicone rubber coating.
What is Para-Aramid?
Para-aramid fibers, commonly known by trade names like Kevlar, are a type of aramid fiber with high tensile strength and elasticity. These fibers are used extensively in industries requiring materials that can withstand high levels of stress and impact without breaking. Para-aramid fibers are typically found in products where strength, resilience, and resistance to wear are critical factors.
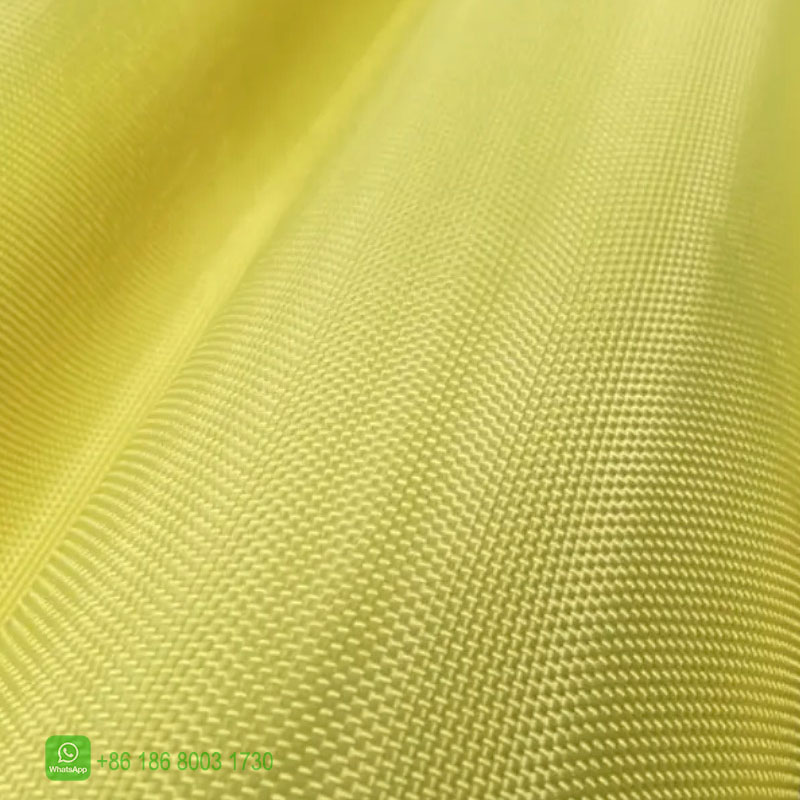
Key Properties of Para-Aramid
- High Tensile Strength: Para-aramid fibers have outstanding tensile strength, allowing them to resist breaking even under extreme stress. This makes them suitable for ballistic applications, ropes, and cables.
- Excellent Abrasion Resistance: With superior abrasion resistance, para-aramid fibers maintain their integrity even in environments where there is a lot of friction.
- High Modulus of Elasticity: They are rigid and maintain their shape under stress, making them ideal for use in composite materials for industries like aerospace and automotive.
- Good Thermal Stability: These fibers can withstand high temperatures, which is why they are often used in firefighter gear and other heat-resistant clothing.
- Low Creep: Para-aramid has minimal deformation under prolonged stress, which is essential in applications requiring consistent structural stability over time.
Due to these properties, para-aramid is commonly found in protective gear, military applications, and products requiring high strength and durability.
What is Meta-Aramid?
Meta-aramid fibers, known by names like Nomex, differ from para-aramid in their molecular structure, which affects their properties. Meta-aramid is particularly known for its superior resistance to heat and flame, making it an excellent choice for applications where fire resistance is paramount.
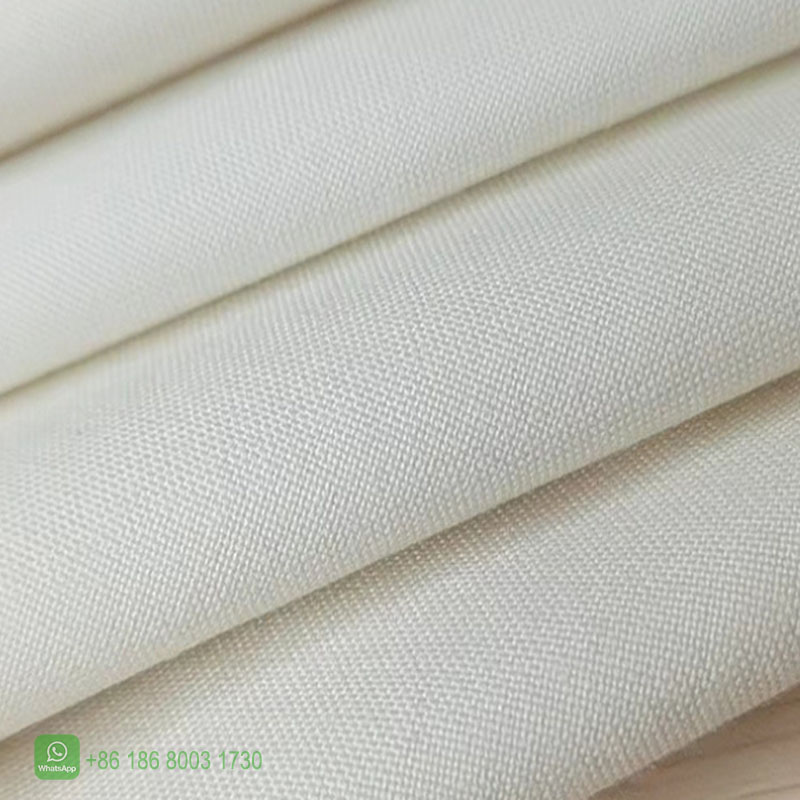
Key Properties of Meta-Aramid
- Superior Thermal Resistance: Meta-aramid fibers have exceptional thermal stability and can withstand direct flame exposure, making them ideal for flame-resistant clothing.
- Good Chemical Resistance: They are highly resistant to a wide range of chemicals, enhancing their durability in challenging environments.
- Moderate Strength: While not as strong as para-aramid, meta-aramid still offers good mechanical properties, making it suitable for applications where extreme strength is not necessary.
- Flexibility and Comfort: Meta-aramid fibers are often softer and more comfortable, making them ideal for protective wear where flexibility and mobility are essential.
- Cost-Effectiveness: Meta-aramid tends to be more affordable compared to para-aramid, providing a balance between performance and budget.
Due to these properties, meta-aramid is commonly used in firefighting suits, industrial protective clothing, and electrical insulation applications.
Para-Aramid vs. Meta-Aramid: Key Differences
To better understand the differences between these two materials, here is a comparative table summarizing their main characteristics:
Property
|
Para-Aramid (e.g., Kevlar)
|
Meta-Aramid (e.g., Nomex)
|
---|---|---|
Strength
|
Higher tensile strength
|
Moderate tensile strength
|
Thermal Stability
|
Good but lower than Meta-Aramid
|
Excellent
|
Abrasion Resistance
|
Superior
|
Moderate
|
Modulus
|
High
|
Lower
|
Applications
|
Ballistics, ropes, cables
|
Fire-resistant clothing
|
Important Features | Extremely strong | High heat resistance |
Cost | $$$$ | $$$ |
This comparison illustrates the unique advantages of each type of aramid, allowing manufacturers to choose the best material based on application needs.
Advantages of Para-Aramid over Meta-Aramid
- Higher Strength: With a much higher tensile strength, para-aramid fibers are more suitable for applications where maximum durability is essential, such as in ballistic protection and high-strength cables.
- Excellent Abrasion Resistance: Para-aramid’s resistance to wear and tear makes it ideal for harsh industrial environments where friction and abrasion are common.
- Low Creep and High Modulus: Its resistance to deformation under stress is valuable in automotive and aerospace industries, where material stability under force is critical.
- High Energy Absorption: Para-aramid is used in ballistic armor because it absorbs and disperses energy efficiently, providing enhanced protection against impacts.
- Enhanced Chemical Resistance: Para-aramid fibers are resistant to a broader range of chemicals, making them suitable for corrosive environments.
- Superior Thermal and Flame Resistance: Meta-aramid is better suited for applications involving high heat and flame exposure, such as firefighter suits and industrial protective clothing.
- Cost-Effectiveness: When extreme tensile strength is unnecessary, meta-aramid provides a more affordable alternative without compromising essential protective qualities.
- Comfort and Flexibility: Meta-aramid fibers are often softer and more comfortable for prolonged wear, making them ideal for personal protective equipment.
Choosing Between Para-Aramid and Meta-Aramid After Silicone Rubber Coating
Applying a silicone rubber coating to aramid fabrics enhances their properties, especially in terms of thermal resistance, water repellency, and durability. This coating provides an added layer of protection, making aramid fabrics even more versatile for industrial and protective applications.
Benefits of Silicone Rubber Coating on Aramid Fabrics
- Improved Thermal Resistance: Silicone rubber can withstand temperatures up to 200°C or more, providing added heat protection for both para-aramid and meta-aramid fabrics.
- Enhanced Durability: The coating makes the fabric resistant to abrasion and wear, extending its lifespan in demanding environments.
- Water and Chemical Resistance: Silicone is inherently water-repellent and provides chemical resistance, which is beneficial in corrosive or damp environments.
- Flexibility and Ease of Use: The silicone coating maintains the fabric’s flexibility, making it suitable for applications that require both durability and ease of handling.
How to Choose the Right Coated Fabric
To choose between para-aramid and meta-aramid with silicone coating, consider the following application-based guidelines:
- For High-Strength Requirements: Opt for para-aramid coated with silicone if the application involves high stress, tensile strength, or abrasion resistance, such as in ballistic protection or heavy-duty manufacturing equipment.
- For Flame-Resistant Applications: Meta-aramid coated with silicone is preferable when fire resistance and heat exposure are primary concerns, as seen in firefighting and industrial uniforms.
- For Chemical and Environmental Resistance: Silicone-coated para-aramid offers better chemical and environmental resistance, making it ideal for industries like petrochemical and waste management.
Real-World Examples of Silicone-Coated Aramid Fabric Applications
- Aerospace: Silicone-coated para-aramid is used in the aerospace industry for high-strength components exposed to high friction and stress.
- Firefighting Gear: Meta-aramid coated with silicone is essential in firefighting suits, providing heat resistance and flexibility required in extreme conditions.
- Electrical Insulation: Both para-aramid and meta-aramid coated with silicone serve as insulators for electrical components, adding durability and resistance to heat and chemicals.
Conclusion
In summary, both para-aramid and meta-aramid fabrics offer unique advantages, with para-aramid excelling in strength and abrasion resistance, and meta-aramid leading in flame resistance and cost-effectiveness. Applying a silicone rubber coating to either fabric enhances its durability, water resistance, and heat tolerance, making these materials more versatile across various industries.
Choosing between para-aramid and meta-aramid ultimately depends on your specific application needs. For projects requiring exceptional strength and abrasion resistance, silicone-coated para-aramid is the ideal choice. For applications where heat resistance and flexibility are crucial, silicone-coated meta-aramid provides reliable performance at a more accessible cost.
By assessing your needs and understanding the properties of these aramid fabrics, you can make a choice that ensures safety, durability, and cost-effectiveness in any industrial setting.