Your Trusted Source for High-Temperature Hoses
YEEDAH is a leading manufacturer High-Temperature Hoses in China, specializing in the development and production of high-temperature flexible duct hoses. Our unwavering commitment to quality has earned us trusted partnerships with prominent brands across Europe and the U.S.
As a vertically integrated manufacturer, we offer a full range of standard and custom flexible hoses. Our product line includes double-layer (2 ply) and single-layer (1 ply) silicone rubber hoses as well as double-layer (2 ply) and single-layer (1 ply) neoprene rubber hoses, ensuring reliable performance in the most demanding applications.
Your Trusted Source for High-Temperature Hoses
YEEDAH is a leading manufacturer High-Temperature Hoses in China, specializing in the development and production of high-temperature flexible duct hoses. Our unwavering commitment to quality has earned us trusted partnerships with prominent brands across Europe and the U.S.
As a vertically integrated manufacturer, we offer a full range of standard and custom flexible hoses. Our product line includes double-layer (2 ply) and single-layer (1 ply) silicone rubber hoses as well as double-layer (2 ply) and single-layer (1 ply) neoprene rubber hoses, ensuring reliable performance in the most demanding applications.
When it comes to high-performance industrial solutions, finding a reliable supplier for high-temperature hoses is crucial. YEEDAH, a leading manufacturer in China, specializes in delivering top-quality flexible duct hoses that meet the demands of various industries. With 16 production lines and years of expertise, we cater exclusively to B2B customers, providing flexible hoses that are built to withstand extreme heat and harsh environments.
Superior Quality, Trusted by Industry Leaders
YEEDAH’s high-temperature hoses are engineered to handle the toughest conditions, whether in automotive manufacturing, industrial equipment, or specialized machinery. Our product line includes silicone-coated hoses, neoprene hoses, and aramid fabric ducting, all designed to maintain durability and flexibility even in extreme temperatures. Whether you need a solution for hot air ventilation, exhaust systems, or dryer machine applications, we offer customizable hoses tailored to your specific operational requirements.
We understand that every business has unique needs. At YEEDAH, we specialize in customizing hose dimensions, coatings, and material specifications to meet your project’s exact requirements. Our B2B clients, from automotive companies to industrial manufacturers across the globe, trust us to deliver products that improve performance and efficiency.
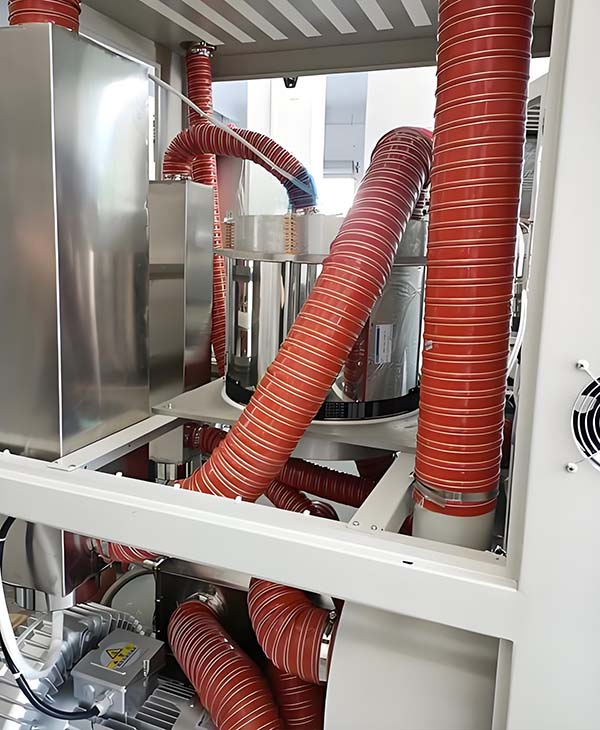
Sizes YEEDAH SUPPLY:TECHNICAL PARAMETER
Size (inch) | ID (mm) | OD (mm) | LENGTH(m) | OVER PRESSURE (bar) | NEGATIVE PRESSURE (bar) | BENDING RADIUS (mm) | WEIGHT (kg/4m) |
---|---|---|---|---|---|---|---|
0.511 | 13 | 16 | 4 | 3 | 0.74 | 10 | 0.35 |
0.63 | 16 | 19 | 4 | 3 | 0.74 | 12 | 0.38 |
0.75 | 19 | 22 | 4 | 3 | 0.73 | 13 | 0.4 |
0.866 | 22 | 25 | 4 | 3 | 0.72 | 14 | 0.5 |
1 | 25 | 28 | 4 | 2.8 | 0.71 | 18 | 0.52 |
1.18 | 30 | 33 | 4 | 2.75 | 0.68 | 19 | 0.58 |
1.26 | 32 | 35 | 4 | 2.7 | 0.65 | 20 | 0.6 |
1.378 | 35 | 38 | 4 | 2.65 | 0.63 | 22 | 0.7 |
1.496 | 38 | 41 | 4 | 2.6 | 0.6 | 24 | 0.76 |
1.575 | 40 | 43 | 4 | 2.6 | 0.6 | 26 | 0.8 |
1.654 | 42 | 45 | 4 | 2.6 | 0.59 | 26 | 0.85 |
1.732 | 44 | 48 | 4 | 2.6 | 0.58 | 27 | 0.95 |
1.772 | 45 | 49 | 4 | 2.6 | 0.58 | 27 | 1 |
1.89 | 48 | 52 | 4 | 2.6 | 0.52 | 31 | 1.05 |
2 | 51 | 55 | 4 | 2.6 | 0.52 | 31 | 1.1 |
2.087 | 53 | 57 | 4 | 2.5 | 0.48 | 32 | 1.2 |
2.244 | 57 | 61 | 4 | 2.5 | 0.48 | 34 | 1.26 |
2.362 | 60 | 64 | 4 | 2.5 | 0.48 | 34 | 1.32 |
2.5 | 63 | 67 | 4 | 2.4 | 0.46 | 37 | 1.4 |
2.756 | 70 | 76 | 4 | 2.1 | 0.44 | 40 | 1.5 |
3 | 76 | 81 | 4 | 2.1 | 0.43 | 43 | 1.6 |
3.15 | 80 | 85 | 4 | 2.1 | 0.42 | 45 | 1.65 |
3.268 | 83 | 88 | 4 | 2.1 | 0.41 | 47 | 1.72 |
3.5 | 90 | 94 | 4 | 2 | 0.4 | 50 | 2.58 |
4 | 102 | 107 | 4 | 1.9 | 0.35 | 56 | 3.2 |
4.252 | 108 | 113 | 4 | 1.8 | 0.33 | 60 | 2.1 |
4.33 | 110 | 115 | 4 | 1.8 | 0.33 | 60 | 2.2 |
4.528 | 115 | 120 | 4 | 1.5 | 0.3 | 63 | 3 |
5 | 127 | 133 | 4 | 1.5 | 0.23 | 70 | 3.16 |
5.236 | 133 | 139 | 4 | 1.4 | 0.22 | 71 | 3.25 |
5.55 | 141 | 147 | 4 | 1.3 | 0.2 | 76 | 3.5 |
5.905 | 150 | 156 | 4 | 1.2 | 0.17 | 82 | 3.6 |
6 | 152 | 158 | 4 | 1.2 | 0.17 | 82 | 3.8 |
6.3 | 159 | 165 | 4 | 1.1 | 0.16 | 86 | 3.9 |
6.456 | 164 | 170 | 4 | 1.1 | 0.14 | 89 | 4 |
6.654 | 169 | 176 | 4 | 1.1 | 0.14 | 89 | 4.2 |
7.008 | 178 | 185 | 4 | 1 | 0.12 | 94 | 4.6 |
7.087 | 180 | 187 | 4 | 1 | 0.12 | 95 | 4.6 |
8 | 203 | 210 | 4 | 0.7 | 0.09 | 108 | 4.8 |
8.622 | 219 | 226 | 4 | 0.6 | 0.08 | 115 | 5.5 |
10 | 254 | 261 | 4 | 0.5 | 0.07 | 133 | 6 |
12 | 305 | 313 | 4 | 0.5 | 0.07 | 159 | 7.5 |
customized services
Beyond our standard offerings, we proudly offer customized services tailored to individual processing requirements. Our customization capabilities extend up to different thicknesses and layers of hose. Including fluororubber hose, and multi-layered silicone ducting.
Package Solution For Option
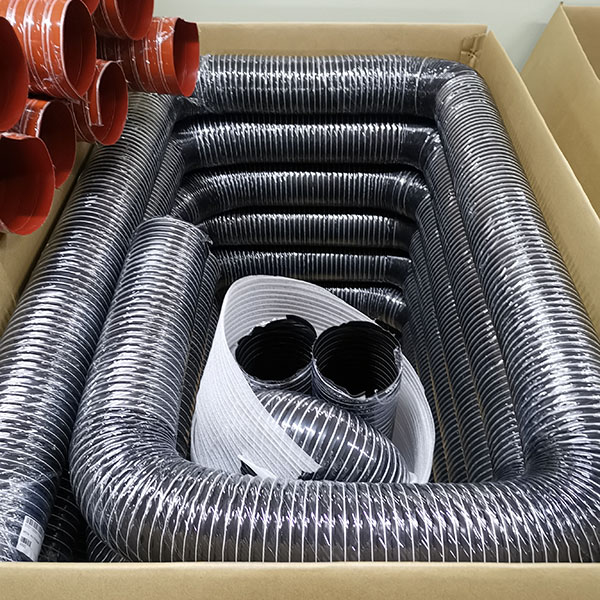
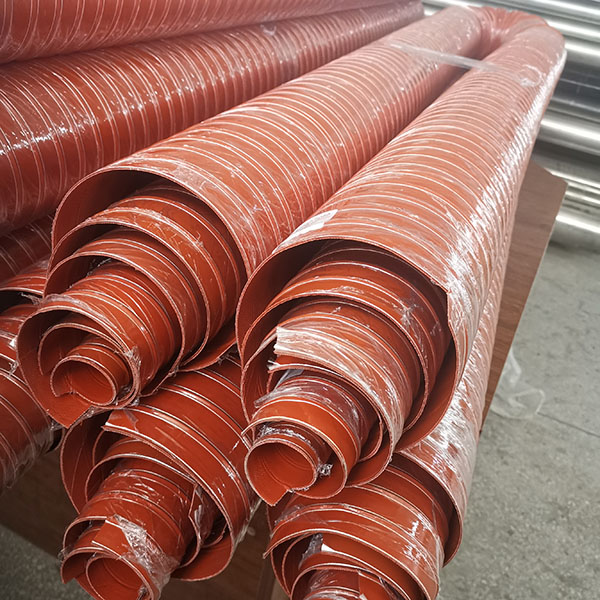
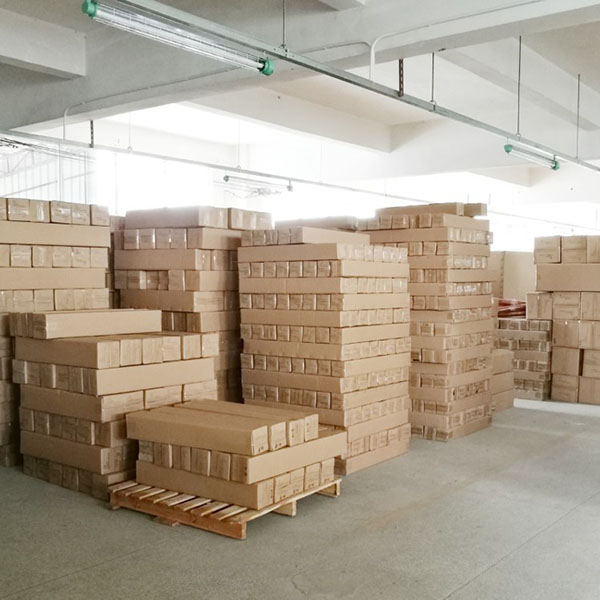
Our Workshop
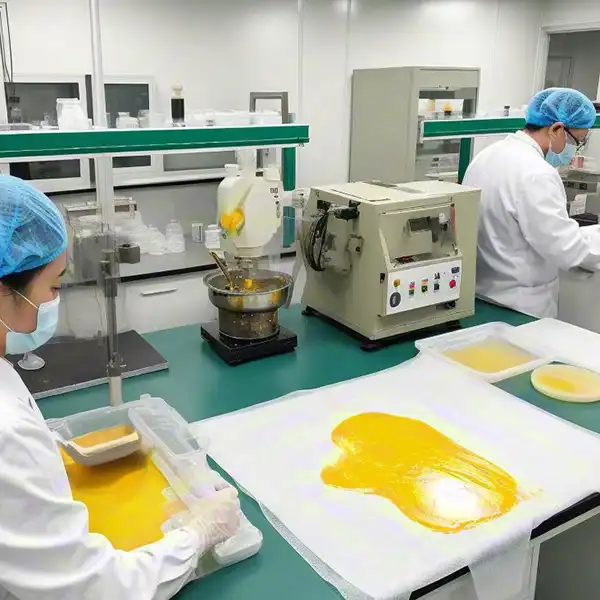
R&D Department
We believe: “R&D: driving progress”
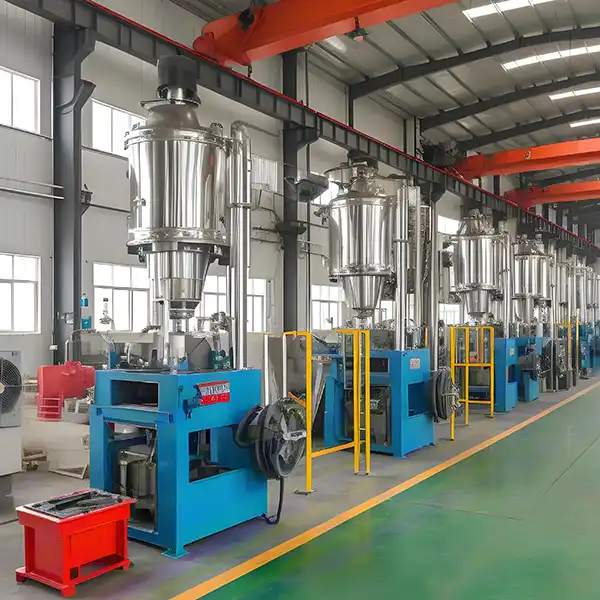
Vulcanization workshop
From Raw Materials to Finished Goods, Precision Manufacturing: Vulcanization Excellence
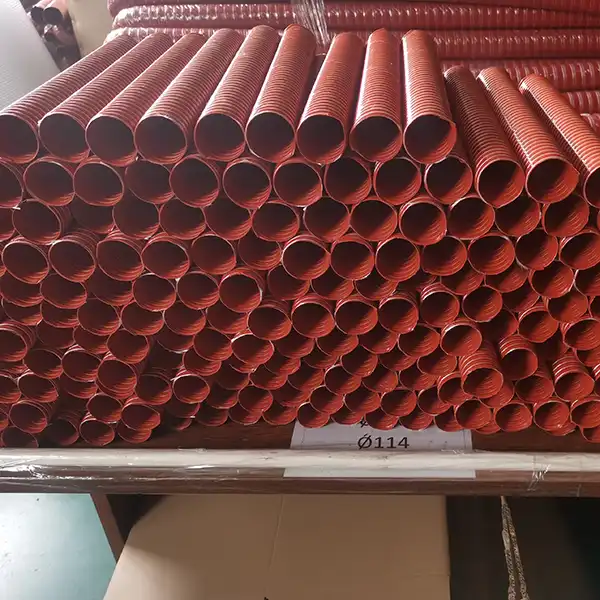
Custom cutting
Custom Solutions Tailored to Your Needs
Let’s talk about your Flexible Hose needs
Please provide the material, size, thickness, and application you want to process, along with the functions you need (e.g, cuffs, thickness , marking). The drawing is required for special items. With this information, we’ll quickly respond with detailed solutions and quotes. Get now!
When choosing silicone hose and neoprene hose need to consider
#. Silicone-Coated Fiberglass Fabric Hoses
These tubes are made by coating fiberglass fabric with a layer of silicone, resulting in a product that has excellent high-temperature resistance and flexibility.
Advantages of Silicone-Coated Fiberglass Hoses
Temperature Resistance: Silicone-coated tubes are highly resistant to extreme temperatures. They can typically withstand temperatures from -60°C to 260°C (-76°F to 500°F), making them ideal for high-heat environments such as exhaust systems, engine compartments, and high-temperature ventilation.
Flame Resistance: Silicone is naturally flame-retardant, and when combined with fiberglass, it creates a barrier that can resist sparks, flames, and molten metal splashes. This makes silicone-coated fiberglass tubes ideal for use in fire-prone environments.
Weather and UV Resistance: Silicone offers excellent resistance to weathering, including UV exposure, ozone, and extreme weather conditions. This makes it suitable for outdoor applications and long-term exposure to the elements.
Chemical Resistance: Silicone is moderately resistant to chemicals, including oils, water, and some solvents. It maintains its integrity even when exposed to moisture or light chemicals.
Flexibility and Durability: Silicone-coated tubes are flexible, making them easy to install, even in complex systems. They also maintain flexibility over a wide temperature range without becoming brittle.
Insulation Properties: Silicone is a good electrical insulator, which makes these tubes suitable for applications where electrical resistance and heat insulation are required.
Applications
- Automotive exhaust systems
- Aircraft and aerospace components
- High-temperature ventilation and duct systems
- Fireproof environments and welding facilities
- Electrical insulation and heat protection
#. Neoprene-Coated Fiberglass Fabric Hoses
Neoprene-coated fiberglass tubes are constructed with a layer of neoprene applied to fiberglass fabric. Neoprene has a different set of properties compared to silicone, which makes it suitable for certain specialized applications.
Advantages of Neoprene-Coated Fiberglass Hoses
Moderate Temperature Resistance: Neoprene-coated fiberglass hoses can typically handle temperatures ranging from -50°C to 135°C (-58°F to 275°F). While this range is lower than silicone, neoprene is still a viable option for many industrial environments where extreme temperatures are not a concern.
Oil and Chemical Resistance: Neoprene offers excellent resistance to oils, petroleum products, and a broad range of chemicals. This makes neoprene-coated fiberglass tubes ideal for use in industries involving lubricants, fuels, and solvents.
Abrasion Resistance: Neoprene has high resistance to physical wear and tear, including abrasion and punctures, making these tubes more durable in environments with rough handling or heavy mechanical stresses.
Water and Moisture Resistance: Neoprene has excellent water resistance, making it suitable for wet environments or applications where condensation and moisture exposure are a concern.
Cost-Effective: Neoprene-coated fiberglass fabric tubes are generally more affordable than silicone-coated tubes, making them an economical choice for applications where extreme temperature resistance is not required.
Applications
- Industrial and construction ventilation systems
- HVAC systems in environments with oils and solvents
- Equipment insulation in wet or oily conditions
- Marine and offshore applications due to water resistance
- Flexible ducting in chemical plants
How to Choose Between Silicone-Coated and Neoprene-Coated Fiberglass Hoses
1. Temperature Resistance
Choose Silicone-Coated: If your application involves high heat or extreme cold, silicone-coated fiberglass is the better option due to its higher temperature range.
Choose Neoprene-Coated: If the temperature requirements are moderate, neoprene may be sufficient and more cost-effective.
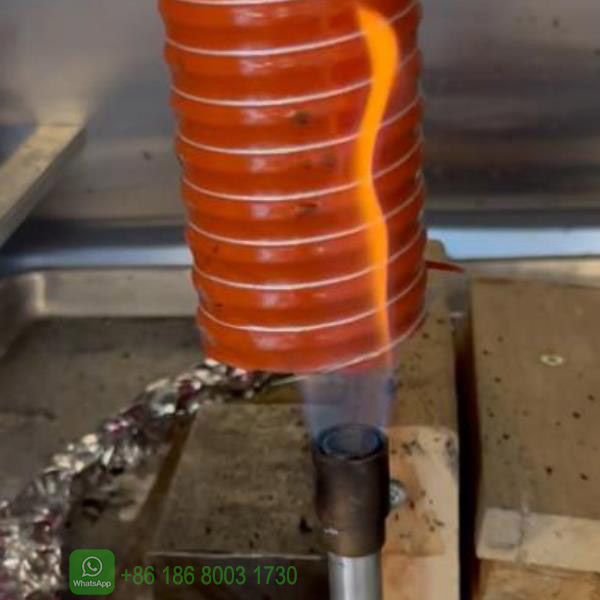
2. Environmental Exposure
Choose Silicone-Coated: For outdoor applications or environments with UV exposure, silicone-coated tubes are ideal due to their superior weather and UV resistance.
Choose Neoprene-Coated: For applications where exposure to oils, chemicals, or solvents is a concern, neoprene-coated tubes are the better option because of their excellent resistance to these substances.
3. Mechanical Durability
Choose Silicone-Coated: If you require flexibility and heat insulation without frequent abrasion, silicone-coated tubes are more durable in high-temperature environments.
Choose Neoprene-Coated: For applications where the tube will undergo mechanical stress or potential abrasion, neoprene-coated tubes offer better physical resistance to damage.
4. Cost
Choose Silicone-Coated: Although more expensive, silicone-coated fiberglass tubes are a worthwhile investment if high-performance and longevity are required in demanding environments.
Choose Neoprene-Coated: If budget is a primary concern and the temperature and environmental conditions are within neoprene’s capacity, this option is more economical.
5. Certifications and Compliance
Both types of tubes often come with certifications such as ISO or UL. Ensure that the product complies with relevant industry standards, particularly for specialized applications like fireproofing or chemical resistance.
In summary, silicone-coated fiberglass tubes are superior for high-temperature, outdoor, and flame-resistant applications, while neoprene-coated fiberglass tubes excel in environments exposed to oils, chemicals, and abrasion, at a lower cost. The choice ultimately depends on your specific operational requirements, budget, and environmental conditions.
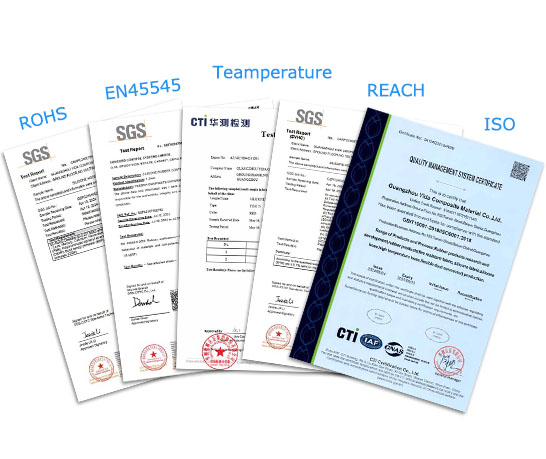
What’s a High-Temperature Air Hose and Why Does It Matter?
What exactly is a high-temperature air hose? The high temp hose is a specialized hose designed to handle extreme heat application. Used for heat air, heater, exhaust gas applications, brake cooling ducts, vehicle engines, dryer vent, granulate transfers, etc. These hoses are essential for industries like manufacturing, automotive, HVAC, and more. Wherever hot air or gasses need to be transferred safely, you’ll find a high-temperature air hose doing its thing.
Why does it matter? Without a reliable hose that can withstand high temperatures, operations could come to a grinding halt. Hoses that melt, crack, or lose flexibility under heat are not just inconvenient—they’re downright dangerous. Industrial settings need components that perform consistently, and high-temp hoses are built to take the heat.
Features that Make High-Temperature Hoses Special
- Heat resistance: Naturally, the primary feature is their ability to withstand high temperatures. Most high-temp hoses can handle air up to 500°F or more.
- Durability: Made from materials like silicone, neoprene, and stainless steel wire reinforcement, these hoses are designed to last in harsh environments.
- Flexibility: Despite the tough conditions, these hoses remain flexible, which is essential when installation requires sharp turns or tight spaces.
- Chemical resistance: Many high-temp hoses also resist oils, solvents, and other industrial chemicals, making them versatile and suitable for various applications.
What will affect high temp hose price?
The price of high-temperature hoses can be influenced by a variety of factors, ranging from material composition to market dynamics. Here are some key elements that typically affect their cost:
Affect | Impact on price |
---|---|
1. Materials Used | |
2. Construction and Layering | |
3. Size and Thickness | |
4. Temperature and Pressure Ratings | |
5. Certifications and Standards Compliance | |
6. Manufacturing Process | |
7. Supply Chain and Availability | |
8. Market Demand and Competition | |
9. Technological Innovations |
How Do High-Temperature Air Hoses Work?
Why these hoses manage to stay flexible when they’re carrying scalding air or steam? It’s all in the materials and the construction. A typical high-temp air hose has single or multilayers, including a heat-resistant exterior and an insulating inner tube. The material composition can vary depending on the application but often includes:
- Silicone: Perfect for maintaining flexibility under high heat, silicone is a favorite for these hoses.
- Neoprene: After silicone, the temperature resistance is lower than silicone, but the material is more wear-resistant than silicone
- Fluororubber: the temperature resistance is better than silicone, long time withstand up to 260 Celsius degrees. And chemical resistance.
- Fiberglass: Often woven into the structure to add additional heat tolerance.
- Stainless steel: Some hoses include a spiral or braided stainless steel wire for reinforcement, boosting durability and strength.
The combination of these materials allows the hose to carry hot air or gases without breaking down or becoming brittle over time. And when you’re dealing with constant high-temperature transfers, this reliability is non-negotiable.
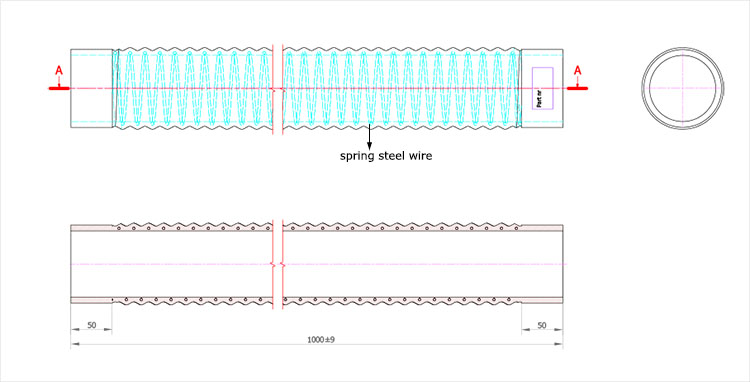
Common Applications for High-Temperature Air Hoses
The variety of industries that rely on high-temp air hoses to keep things running smoothly. Here are some of the most common applications:
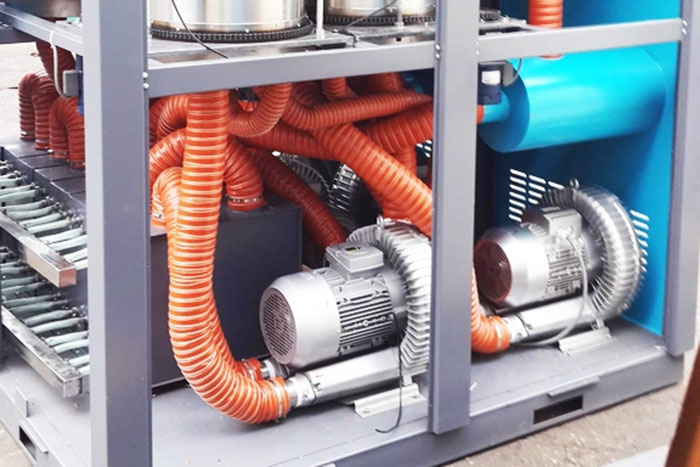
HVAC Systems
Heating, ventilation, and air conditioning systems often require high-temperature hoses to carry hot air or exhaust. Without them, the efficiency of these systems would plummet.
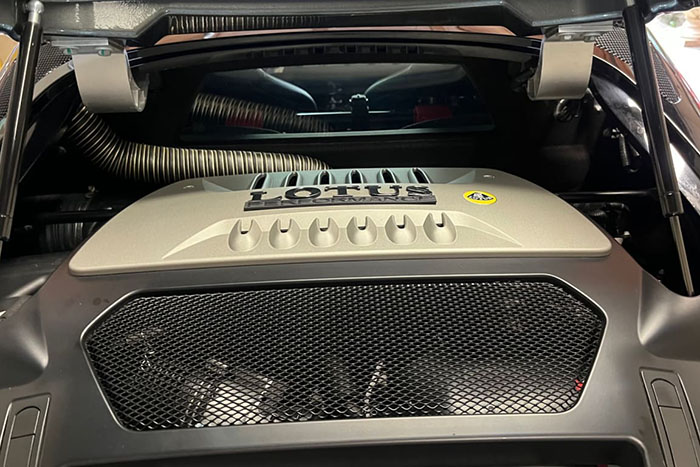
Automotive and Aerospace
From engines to exhaust systems, high-temp hoses are crucial for handling the heat generated by vehicles and aircraft. You’ll find them in everything from heavy-duty trucks to airplanes.
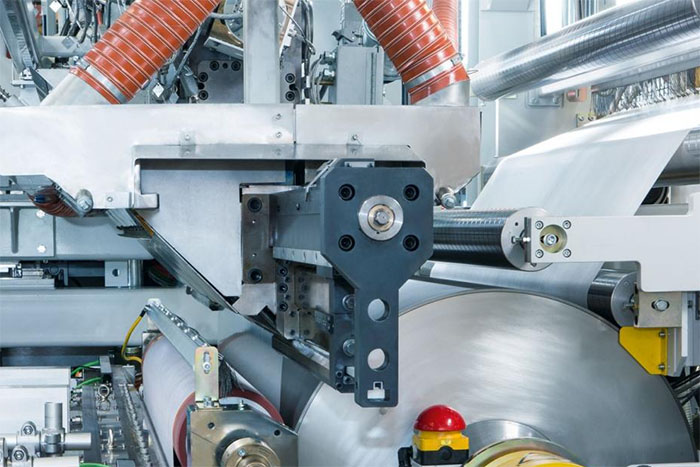
Manufacturing
In industrial settings, high-temperature hoses are indispensable for processes like drying, cooling, and moving materials. They ensure that hot air and gasses can be safely transported without damaging equipment.
Why Flexibility is Crucial in High-Temperature Hoses
- Most industrial applications involve complex systems with plenty of tight spaces. A rigid hose simply wouldn’t cut it. Flexibility allows for easy installation, even in the most cramped environments, ensuring the hose can navigate around corners, bends, and obstacles without compromising performance.
- Moreover, flexibility adds to the hose’s longevity. A rigid hose is more likely to crack or break when exposed to constant vibrations or mechanical stress, while a flexible one can absorb and dissipate these forces more effectively.
Key Benefits of Using High-Temperature Air Hoses
When it comes down to it, choosing the right hose can save a lot of time, money, and headaches. So, what makes high-temp air hoses the ideal choice for many industries? Here are some key benefits:
High-Temperature Hose Maintenance: Tips for Longevity
To get the most out of high-temperature air hose, regular maintenance is key. Here’s a quick rundown of what should be doing:
- Inspect for wear and tear: High-temp hoses are built to last, but even the best ones can show signs of wear over time. Make it a habit to inspect the hose regularly for cracks, leaks, or stiffness.
- Check the fittings: A hose is only as good as its connections. Loose or corroded fittings can compromise the hose’s performance and lead to dangerous situations.
- Clean regularly: Keeping the hose clean can prevent buildup of gunk or chemicals that could degrade the materials over time.
- Avoid sharp bends: Although these hoses are flexible, consistently bending them at sharp angles can cause unnecessary stress and shorten their lifespan.
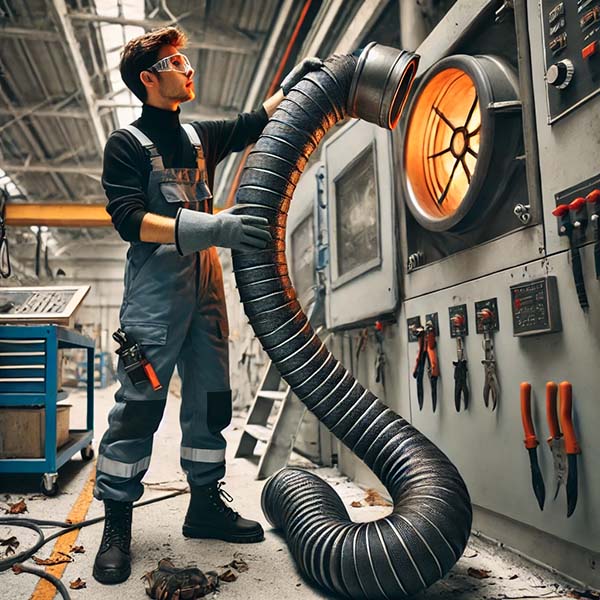
Why High-Temperature Air Hoses are a Must-Have
High-temperature air hoses are an essential part of any industrial setup where heat, durability, and flexibility matter. Whether you’re dealing with automotive exhaust systems, HVAC installations, or high-heat manufacturing processes, these hoses can take the heat—literally. They’re built to withstand extreme temperatures, resist chemicals, and remain flexible, making them the ideal choice for countless applications.
But like any tool, getting the most out of your high-temp hose means choosing the right one for the job and maintaining it properly. So don’t let heat get in the way of your operation—invest in a high-temperature air hose and keep things running smoothly.
FAQs About High-Temperature Air Hoses
A Manufacturing Partner You Can Rely On
Ready to start? Share your requirements, get tailored solutions and quotes within 24 hours, and begin mass production with confidence.
Get in touch for more information or a detailed quote.