Your Trusted Source for Flexible Duct Connector
YEEDAH is a leading manufacturer of custom flexible air duct connectors in China. YEEDAH offers a variety of connectors that can be customized to meet specific requirements, ensuring they are suitable for various applications, including residential, commercial, and industrial settings. Including flexible duct connector, TDF Flange and expansion joints.
Your Trusted Source for Flexible Duct Connector
YEEDAH is a leading manufacturer of custom flexible air duct connectors in China. YEEDAH offers a variety of connectors that can be customized to meet specific requirements, ensuring they are suitable for various applications, including residential, commercial, and industrial settings. Including flexible duct connector, TDF Flange and expansion joints.
YEEDAH Fabric Workshop
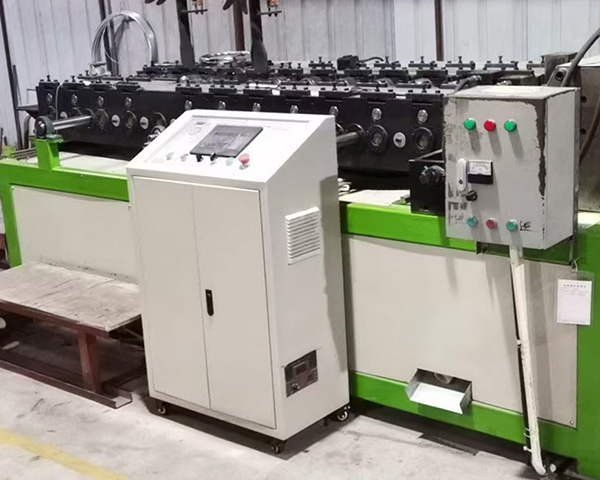
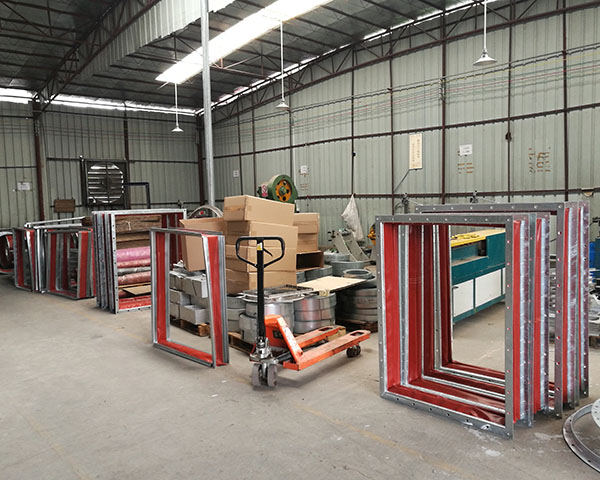
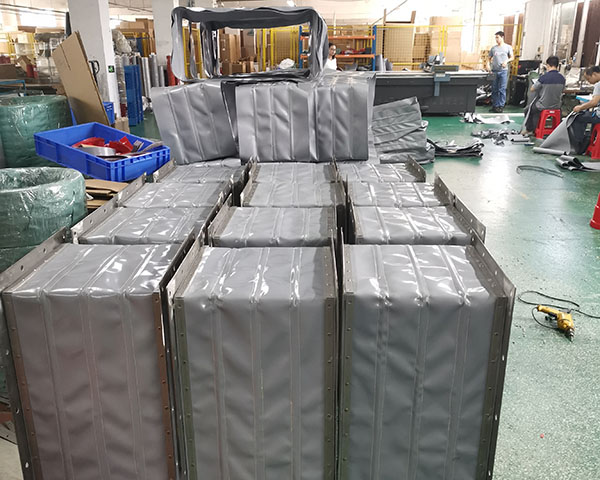
All You Need to Know About Flexible Air Duct Connectors
Flexible air duct connectors are crucial components in the HVAC system, providing essential flexibility and vibration dampening to enhance system efficiency and longevity. In this guide, we’ll delve deep into the structure of these connectors, the materials commonly used, their advantages, and best practices for selection and installation. Whether you’re a seasoned professional or a newcomer, this guide will equip you with the knowledge to make informed decisions about flexible duct connectors.
What is a Flexible Air Duct Connector?
Flexible air duct connectors are specialized materials used to connect air ducts securely while isolating vibrations and noises between the equipment and the ductwork. Typically made from a combination of fabrics and metals, these connectors serve as a critical junction point in HVAC systems, allowing for slight movements caused by the operation of the system.A flexible air duct connector is a crucial component in an HVAC system, providing a flexible bridge between rigid ductwork. This flexibility helps to absorb vibrations and prevent noise from spreading through the duct system, making for a quieter and more efficient air flow.
Common Types of Flexible Air Duct Connectors
#1 . Fabric Connectors
#2 . Flexible duct connector
#3 . Expansion joint
#4 . Metal connectors
#5 . Rubber and Plastic Connectors
Benefits of Using Flexible Air Duct Connectors
Enhanced Efficiency
By securing airtight connections and reducing air leaks, flexible duct connectors optimize the airflow and efficiency of HVAC systems.
Noise Reduction
To dampen noise and vibrations. This creates a quieter, more comfortable environment, which is especially important in residential and sensitive commercial settings.
Vibration Isolation
They minimize the transfer of vibrations from HVAC equipment to the building structure.
Flexibility
Accommodates minor misalignments and movements between building components.
Let’s Talk About Your Needs
Please provide the material, size, thickness, and application you want to process, along with the functions you need (e.g, cuffs, thickness , marking). The drawing is required for special items. With this information, we’ll quickly respond with detailed solutions and quotes. Get now!
Key Material Properties for Duct Connectors
Understanding the key material properties for duct connectors is crucial for selecting the right type for your HVAC system. Here are the essential properties to consider:
Flexibility
Flexibility is vital to accommodate slight misalignments and movements within the HVAC system, reducing stress on the ductwork and preventing tear or damage under normal thermal expansion and contraction.
Durability
Durability ensures that the connectors last as long as the ductwork without needing frequent replacements. This reduces maintenance costs and ensures continuous system integrity.
Resistance to Environmental Factors
- Heat Resistance: Connectors must withstand the temperatures they are exposed to, especially in high-temperature applications like furnace ductwork or industrial processes.
- Chemical Resistance: In environments where chemicals are present, such as in industrial applications or laboratories, connectors need to resist corrosion or degradation.
- Moisture Resistance: For systems exposed to humidity or direct moisture, such as in basements or kitchens, moisture resistance is essential to prevent mold growth and material breakdown.

Comparison of Material Options
When selecting the material for duct connectors, considering the environment and specific application needs is crucial. Here’s a comparison of common materials:
Material | Thickness (mm) | Working Temp | Pros | Cons | Cost |
---|---|---|---|---|---|
Vinyl (PVC) | 0.4~0.55 | -20~80 ℃ | Light weight, cost-effective, flexible, good moisture resistance, strong tensile strength, suitable for light to moderate heating and cooling systems. | Limited heat resistance, can off-gas VOCs in high heat, less durable compared to other materials. | |
Neoprene | 0.45 | -50~135 ℃ | Excellent flexibility, oil resistant, very good chemical and heat resistance, durable, suitable for a wide range of applications including industrial settings. | More expensive than vinyl and silicone, can be heavier, which might require more secure installation. | |
Silicone | 0.4~1.2 | -60~260 ℃ | Superior heat resistance, excellent flexibility, inert and does not react with most chemicals, ideal for extreme temperature applications. | High cost, can be over-specified for simple applications, installation requires more care to ensure sealing. |
Choosing According to Application Needs
Selecting the right material for your flexible duct connectors depends largely on the specific conditions and requirements of your application
When choosing a material, consider not only the environmental conditions but also the operational requirements like air speed, pressure, and the presence of oils, greases, or other substances that could impact the longevity and performance of the duct connectors. Always consult with HVAC professionals to ensure that the material selected meets both the safety standards and efficiency needs of your specific system.
Applications of Flexible Air Duct Connectors
Where are They Used?
Flexible air duct connectors are versatile components used in various settings within HVAC systems to enhance functionality and performance. Their primary function is to provide a flexible join between rigid components, helping to absorb vibration, reduce noise, and accommodate thermal expansion and misalignment. Here are some key applications of flexible air duct connectors:
Residential HVAC Systems
1. Air Distribution Efficiency:
- In residential settings, flexible duct connectors are crucial for reducing noise and vibration from the central air conditioning units as air flows through the system, contributing to a quieter home environment.
2. Ease of Installation:
- Flexible connectors simplify the installation process in complex layouts where rigid ducts would be difficult to align and connect directly.

Commercial Buildings
1. Large Scale HVAC Operations:
- Commercial buildings, including offices, schools, and hospitals, use large HVAC systems that benefit significantly from the vibration isolation provided by flexible duct connectors, ensuring a more stable and quiet operation conducive to work and learning environments.
2. Air Quality and Comfort:
- These settings demand consistent indoor air quality and thermal comfort, roles that flexible duct connectors support by maintaining efficient airflow and sealing against leaks.
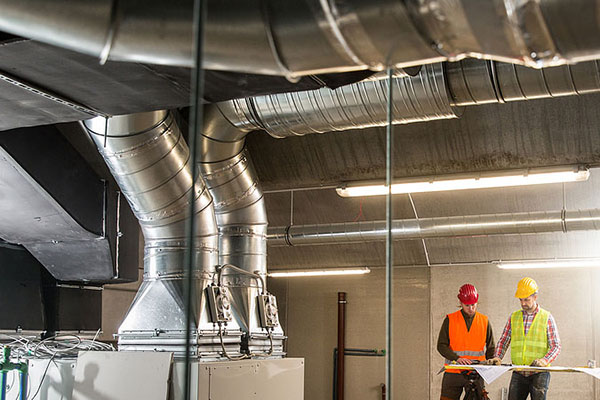
Industrial Applications
1. High-Demand Systems:
- Industrial facilities often have HVAC systems that operate under extreme conditions—handling high temperatures, corrosive chemicals, or both. Flexible duct connectors made from specialized materials like silicone or neoprene can withstand these harsh environments.
2. Vibration Isolation in Machinery:
- In factories with heavy machinery, flexible duct connectors help isolate vibrations, not only within the HVAC system but also from the equipment to the air ducts, preserving the integrity of the ductwork and machinery performance.
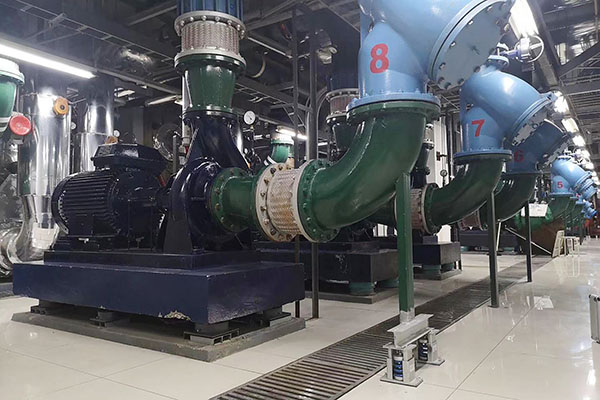
Specialty Applications
1. Ventilation in Harsh Environments:
- Flexible duct connectors are also used in applications requiring ventilation in harsh or corrosive environments, such as chemical processing plants or outdoor installations, where they must resist environmental degradation.
2. Mobile and Temporary Installations:
- In temporary structures like event tents or mobile homes, where installation flexibility and durability are crucial, flexible duct connectors provide an effective solution for temporary heating, cooling, and air handling needs.
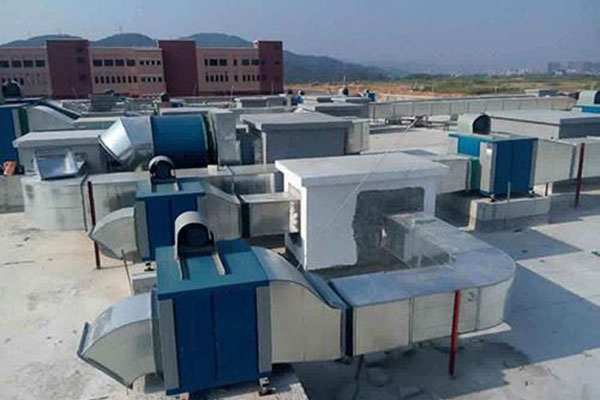
Ventilation Systems
1. Energy Recovery and HVAC Efficiency:
- Flexible duct connectors are used in energy recovery systems where maintaining airtight and vibration-free connections improves system efficiency and performance.
2. Safety and Fire Prevention:
- In systems requiring fire-resistant materials, specially designed flexible connectors help prevent the spread of flames or smoke through ductwork in the event of a fire.
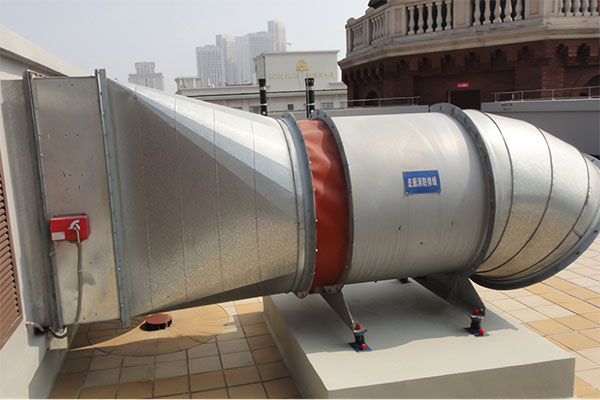
Architectural and Aesthetic Applications
1. Complex Architectural Designs:
- Modern architecture often features complex, non-linear designs where flexible duct connectors can facilitate creative and effective duct routing without compromising the architectural integrity.
2. Adaptation to Building Movement:
- In high-rise buildings or structures subject to movement, flexible connectors accommodate slight shifts without damaging the HVAC system, ensuring long-term operation despite dynamic physical stresses.
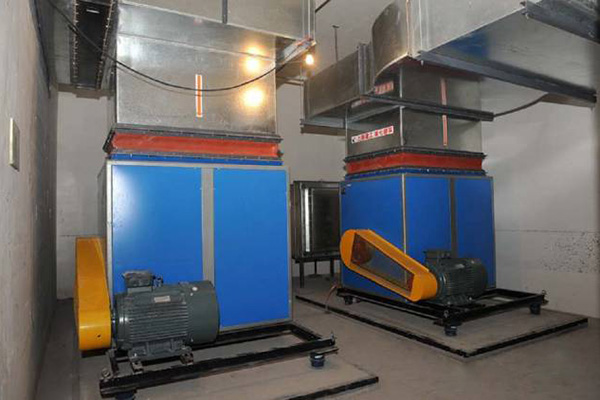
These varied applications underscore the importance of selecting the appropriate type and material of flexible duct connectors to meet specific operational demands and environmental conditions, ensuring the longevity and efficiency of HVAC systems across different settings.
Installation Guidelines for Flexible Duct Connectors
Proper installation of flexible duct connectors is crucial for the optimal performance of HVAC systems. Incorrect installation can lead to reduced system efficiency, increased noise, and even system failure. Here are step-by-step guidelines to ensure that flexible duct connectors are installed correctly:
Preparing for Installation
1. Gather Tools and Materials: Before starting, make sure you have all necessary tools and materials. Commonly needed items include:
- Duct connector itself
- Sheet metal screws
- Duct tape or a specialized duct sealant
- Metal snips
- Screwdriver or drill
- Measuring tape
2. Measure the Ductwork: Accurately measure the ductwork where the connector will be installed. This ensures the connector fits perfectly, avoiding unnecessary strain or gaps.
3. Check Compatibility: Ensure the connector material is suitable for the temperature and chemical conditions of the ductwork environment.
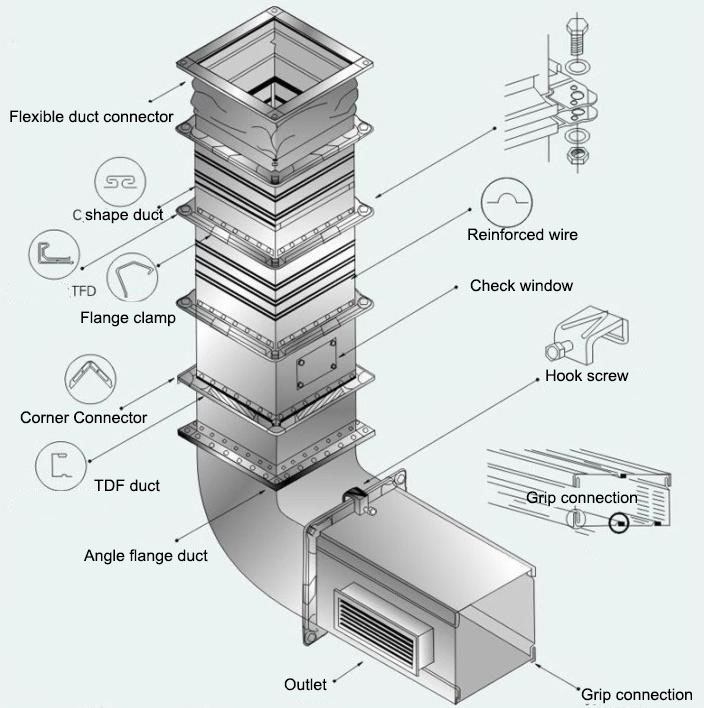
Step-by-Step Installation Process
- Prepare the Duct Ends: Clean and smooth the edges of the ducts where the connector will attach. Any sharp or uneven edges can damage the connector.
- Attach the Metal Flanges: Most flexible duct connectors come with metal flanges that need to be securely attached to the ductwork. Fasten these with sheet metal screws, spacing them evenly around the perimeter.
- Install the Flexible Section: Attach the flexible part of the connector to the flanges. Ensure it is not twisted or kinked, as this can restrict airflow and cause the system to operate inefficiently.
- Secure with Fasteners: Use screws or clamps to secure the flexible section to the flanges. Ensure a tight fit to prevent air leaks but avoid over-tightening, which can tear the material.
- Seal the Connections: Use duct tape or a specialized duct sealant to seal the joints between the ductwork and the metal flanges. This step is crucial to prevent air leaks which can significantly impact system efficiency.
- Inspect for Proper Alignment: Make sure the ductwork is properly aligned and that there are no stress points on the connector. Misalignment can lead to early wear and tear.
Post-Installation Checks
- Test for Leaks: Once the installation is complete, test the system at normal operating pressures to ensure there are no air leaks. Use smoke pencils or a similar device to detect leaks.
- Check for Noise: Run the system and listen for any unusual noises. Excessive rattling or whistling sounds can indicate loose connections or other issues.
- Perform a Visual Inspection: Ensure that the connector is not compressed or stretched too much, as this can affect its performance. It should be installed neutrally, without tension or compression.
Tips to Avoid Common Mistakes
- Do Not Overstretch: Flexible connectors should not be used to make up for significant gaps between ductwork. They are designed to provide flexibility, not length.
- Avoid Sharp Bends: Ensure that the installation does not create sharp bends in the connector, as this can restrict airflow and reduce efficiency.
- Regular Maintenance: Check connectors during regular HVAC maintenance. Look for signs of wear, corrosion on metal parts, and ensure all seals remain air-tight.
By following these detailed installation guidelines, you can ensure that your flexible duct connectors are installed correctly, providing optimal performance and longevity for your HVAC system.
Maintaining Guidelines for Flexible Duct Connectors
Maintaining flexible air duct connectors is crucial for ensuring the long-term efficiency and reliability of HVAC systems. Regular maintenance helps prevent system failures, optimizes energy use, and extends the lifespan of both the ductwork and the HVAC equipment. Here’s a comprehensive guide to maintaining flexible air duct connectors:
Regular Inspection Schedule
1. Visual Inspections:
- Frequency: Conduct visual inspections at least twice a year, typically during the spring and fall before the major heating or cooling seasons begin.
- What to Look For: Check for signs of wear and tear such as cracks, loose parts, fraying, or any visible defects in the connectors. Ensure that connectors are not compressed, twisted, or pulled apart, which can compromise their function.
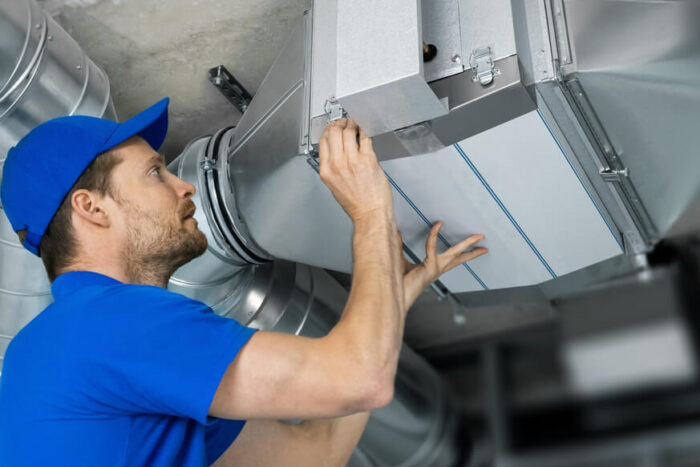
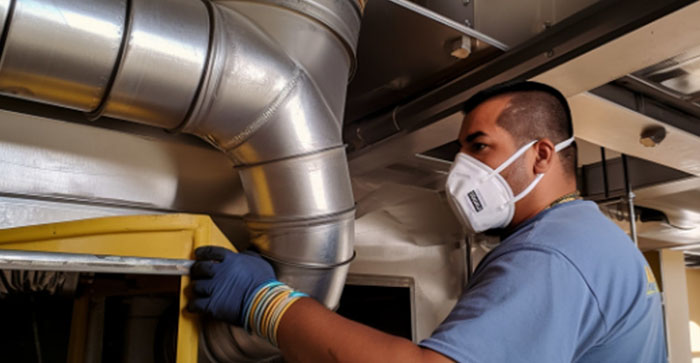
2. Physical Inspection:
- Frequency: Physical inspections should be part of your annual HVAC maintenance routine.
- What to Do: Feel along the connectors for any irregularities. Squeeze them lightly to check for brittleness or areas that may have become stiff, which could indicate degradation of the material.
Cleaning Procedures
1. Dust and Debris Removal:
- Tools Needed: Use a soft brush or a vacuum with a brush attachment.
- Procedure: Gently remove any dust, lint, or debris that has accumulated on the surface of the duct connectors. This prevents blockages and maintains air quality and efficiency.
2. Mold and Mildew Cleaning:
- When Needed: If you notice signs of mold or mildew, which can occur in humid environments.
- Cleaning Solution: Use a mild detergent mixed with water, or a solution recommended by the connector manufacturer that is safe for the material.
- Application: Apply the solution with a cloth or sponge, gently cleaning the affected area without saturating the material.
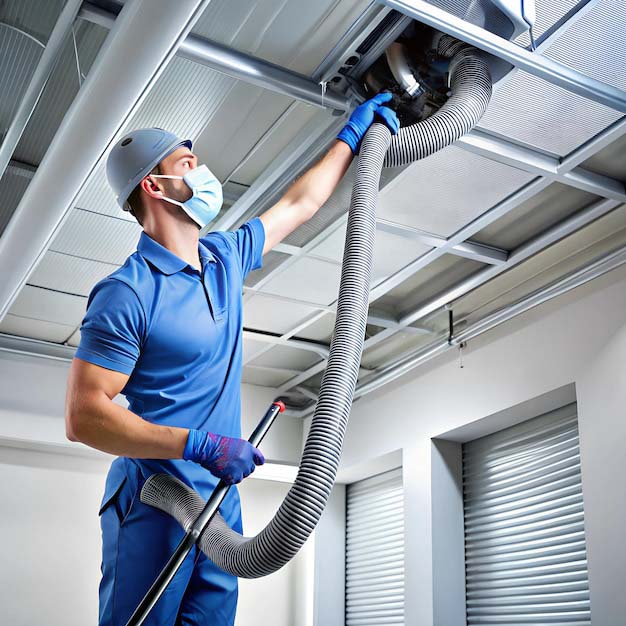
Preventive Measures
1. Ensure Proper Installation:
- Proper installation is key to reducing the need for frequent maintenance. Ensure that flexible duct connectors are installed correctly, without undue stress or stretching.
2. Check for Secure Fittings:
- Regularly check that all fittings and clamps are tight and secure. Loose fittings can lead to inefficiencies and increased wear on the connectors.
3. Avoid Excessive Heat Exposure:
- Ensure that duct connectors are not exposed to temperatures higher than what they are rated for. Excessive heat can accelerate material degradation.
Troubleshooting Common Issues
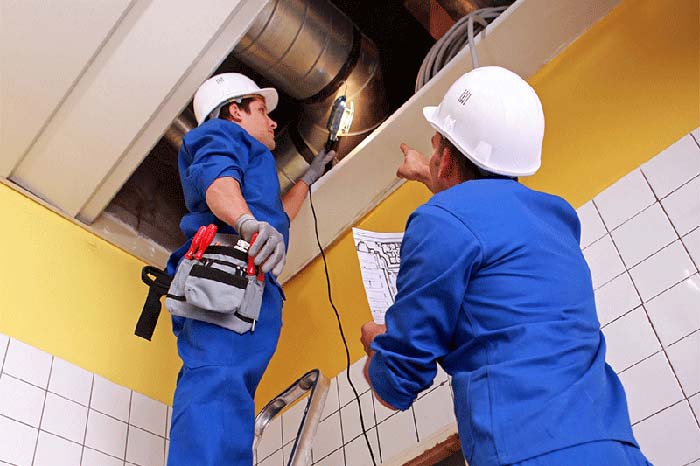
Long-Term Care Tips
- Replacement Planning: Even with the best maintenance, flexible duct connectors will eventually need replacement. Plan for this by keeping records of installation dates and any maintenance issues, and inspect older parts more frequently as they near the end of their expected lifespan.
- Upgrade Options: Consider upgrading to higher-quality or more suitable materials as replacements for better performance and longer life, especially if the system requirements have changed or if there have been issues with the current materials.
By adhering to these maintenance guidelines, you can ensure that flexible air duct connectors continue to function effectively, supporting the overall health and efficiency of your HVAC system. Regular maintenance not only helps in prolonging the life of the connectors but also contributes to maintaining a comfortable and safe environment indoors.
By adhering to these maintenance guidelines, you can ensure that flexible air duct connectors continue to function effectively, supporting the overall health and efficiency of your HVAC system. Regular maintenance not only helps in prolonging the life of the connectors but also contributes to maintaining a comfortable and safe environment indoors.