Table of Contents
How to Make Silicone-Coated Fabric: Step-by-Step Guide
Introduction
Silicone-coated fabric is a versatile material widely used in industries such as automotive, medical, and outdoor equipment manufacturing. Its unique properties—such as water resistance, flexibility, and thermal stability—make it ideal for applications requiring both strength and adaptability. Creating silicone-coated fabric yourself can be cost-effective and customized to your needs. In this guide, we’ll walk you through the entire process, from choosing materials to applying the final coating and curing.
Materials Needed
Before beginning, gather the following materials and equipment:
- Fabric material (e.g., cotton, polyester, fiberglass, or nylon blend)
- Liquid silicone rubber (LSR) or solid silicone rubber (SSR)
- Catalyst (for curing the silicone)
- Mixing container
- Paintbrush or roller
- Oven or curing equipment
- Ventilation equipment (if working indoors with fumes)
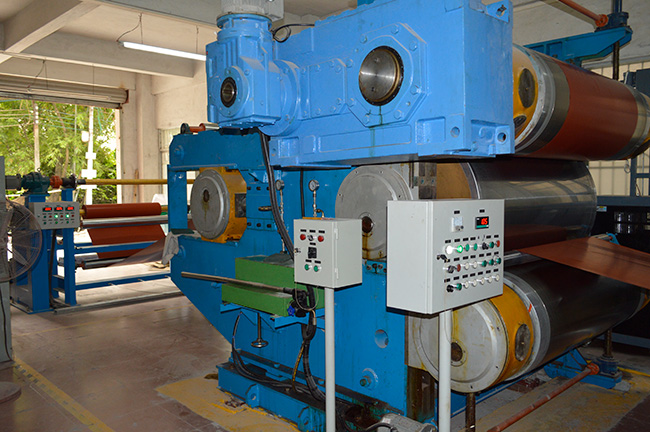
Steps to Make Silicone-Coated Fabric
1. Prepare the Fabric
Choosing the appropriate base fabric for silicone-coated fabric production, depending on its intended use. Fiberglass is often selected for its excellent thermal insulation and fire resistance, making it ideal for safety gear and industrial applications. Polyester provides good strength, durability, and chemical resistance, suited for outdoor and automotive uses. Nylon, known for its exceptional strength and elasticity, is typically used in applications where wear resistance and flexibility are needed.
The base fabric you choose will impact the durability and functionality of the final product:
- Fiberglass: Great for thermal insulation and fire resistance, ideal for safety gear and industrial uses.
- Polyester: Provides strength and chemical resistance, perfect for outdoor and automotive applications.
- Nylon: Known for elasticity and wear resistance, ideal for applications requiring flexibility.
Proper preparation of the base fabric is essential to ensure successful silicone coating. This process starts with thorough cleaning to remove any impurities that could inhibit the adhesion of the silicone. After cleaning, the fabric must be completely dried to prevent moisture from affecting the curing of the silicone. Pre-treatment processes such as heat setting or chemical treatments may also be employed to enhance the fabric's bonding capabilities with silicone. These steps are critical for achieving a high-quality, durable silicone-coated fabric. Make sure your fabric is clean and free of any dust, dirt, or oils that could interfere with silicone adhesion. Cut the fabric to the desired size and shape.
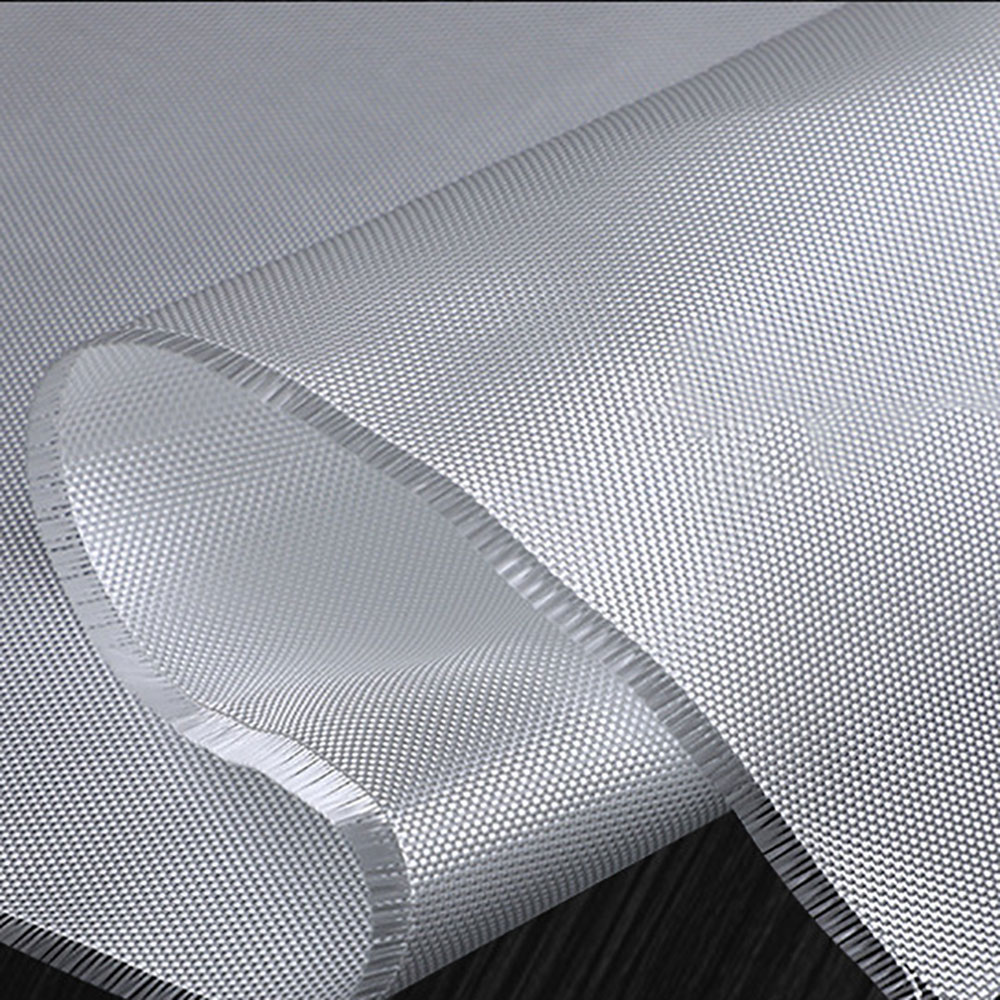
2. Mix the Silicone Rubber
In a well-ventilated area, mixing silicone rubber for coating involves a precise balance of polymer base and a curing agent. The specific ratio and mixing instructions may vary depending on the product you're using.The key is to achieve the right viscosity for application, which varies based on the method used (e.g., spraying, dipping). This is critical: follow the exact ratio provided, as varying amounts can impact curing time and coating flexibility. Common mixing errors include not thoroughly blending the components or incorrect proportions, which can lead to an uneven cure and poor adhesion. Utilizing high-quality mixers and following strict mixing guidelines can help avoid these issues. Tip: Wear gloves and safety goggles to protect yourself while handling the silicone and catalyst.
3. Catalysts and Additives
Catalysts are crucial in the silicone mixture as they trigger the curing process, converting the liquid silicone into a durable, elastic coating. The type and amount of catalyst used directly influence the curing speed and the final properties of the coated fabric. Additives may also be included to enhance specific features such as color, UV resistance, or flame retardancy. Understanding the role of each component in the silicone mixture is essential for tailoring the product to meet specific application requirements.
4. Apply the Silicone Coating
Use a paintbrush or roller to evenly apply the mixed silicone rubber to one side of the fabric. You can apply multiple coats for added thickness and durability,allowing time to partially dry between each coat. Ensure that the silicone is spread evenly and covers the entire surface you want to coat.
Different application techniques are suited for varying requirements of silicone coating. Knife-over-roll offers precision in coating thickness, ideal for high-quality fabric finishes. Dip coating is simpler and suitable for heavy coatings, commonly used for industrial fabrics. Rotary screen printing allows patterned and selective coating, perfect for functional and decorative textiles.
Tip for Even Coating: Keep strokes consistent and check for any missed spots or uneven areas. Using a squeegee can help to achieve a more even spread if needed.
Ensuring even application of silicone involves controlling the viscosity of the silicone mixture and the speed of the application process. Key tips include maintaining consistent tension in the fabric during application and using well-calibrated equipment to apply the silicone. Avoiding defects such as air bubbles or uneven thickness can be achieved by adjusting the distance between the knife and the roller, and ensuring the fabric passes smoothly through the coating device. Proper drying and curing after application also help prevent imperfections and ensure a uniform coat.
5. Curing and Cooling
Curing Process: The silicone coated fabric is placed in an oven or curing equipment and cured to the recommended temperature and curing time specified by the silicone manufacturer. This process is called vulcanization. Curing times can vary, but are typically between 30 minutes and a few hours.
The curing process is critical to ensuring that the silicone coating adheres well and achieves the desired effect. This involves setting the correct time and temperature, depending on the type of silicone used and the characteristics of the fabric. Typically, the process requires a controlled heating environment where the temperature is evenly distributed to promote uniform curing.
Pro Tip:Use a controlled heating environment to ensure an even cure. Avoid overheating, which can compromise the fabric's integrity.
Cooling Process: After curing, the silicone coated fabric must be properly cooled to prevent deformation or shrinkage. Best practices include gradual cooling in a controlled environment to avoid rapid temperature changes that can cause the fabric to warp. Ensuring that the fabric lies flat or hangs without overlapping during the cooling process also helps maintain the quality and size of the coated material. Inspect the silicone coated fabric for any defects or uneven coating. If necessary, apply more coats and repeat the curing process.
6.Final Processing
After achieving the desired silicone coating thickness and quality, you can further process the fabric as needed. This may include cutting, sewing, or assembling it into the final product.
7.Quality Control
Inspection Techniques: Conducting thorough inspections in the production of silicone-coated fabrics involves a detailed examination of the coated material to identify any potential defects such as uneven coating, air bubbles, or improper curing. This can be achieved through visual inspections, tactile tests, and specialized instruments that measure thickness and adhesion quality.
Ensuring Quality: Maintaining high standards throughout the production cycle of silicone-coated fabrics requires implementing a robust quality control system. This includes routine checks at various stages of the production process, from raw material intake to final product review. Employing statistical quality control methods and maintaining a well-trained QC team are essential strategies to ensure every batch of fabric meets the established standards. Ensure that the silicone-coated fabric meets the required quality and performance standards for your intended application.
It's important to note that the specific process and materials may vary depending on the type of silicone rubber and fabric you're using, as well as the intended application. Always follow the manufacturer's guidelines and safety precautions when working with silicone rubber and related chemicals.
Troubleshooting Common Issues:
Solutions and Preventive Measures:
Conclusion
Creating silicone-coated fabric is a multi-step process that, with the right materials and technique, results in a versatile and durable product. From selecting the right materials to ensuring quality control, this guide has covered the essentials to help you achieve a professional finish.
The silicone-coated fabric industry continues to evolve with advancements in smart textiles and sustainability. If you're looking for tailored solutions or industry-grade materials, YEEDAH offers innovative, high-quality products developed over 20 years of experience. Explore YEEDAH’s offerings and boost your projects with our expertise!