Table of Contents
Introduction
In large industrial and commercial HVAC systems, minimizing noise and vibration is crucial to maintaining a comfortable and efficient environment. But, directly connecting duct systems to equipment often leads to excess noise, energy loss, and wear. Flexible duct connectors offer a specialized solution by isolating vibrations, containing air, and reducing system wear—making them essential in modern HVAC setups.
What is a Flexible Duct Connector?
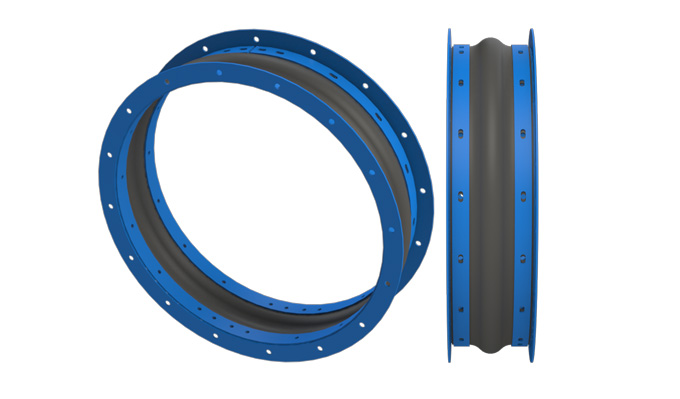
Flexible duct connectors consist of a flexible joint, often fabric-based, fastened between two pieces of sheet metal. Unlike rigid connectors, these components allow for slight movement or alignment adjustments, providing a seamless bridge between the equipment and ductwork.
Key Benefits of Using Flexible Duct Connectors
Flexible duct connectors bring multiple advantages, especially in high-demand environments. Here’s what makes them indispensable:
- Noise and Vibration Reduction: Flexible duct connectors isolate vibrations from fans and blowers, minimizing noise transmitted through ductwork, which is critical for maintaining comfort in large facilities.
- Flexibility and Misalignment Compensation: By allowing slight offsets between equipment and ductwork, flexible duct connectors reduce stress, accommodating for thermal expansion or slight shifts.
- Durability and Energy Efficiency: High-quality materials ensure durability, while proper air containment minimizes energy losses, contributing to overall system efficiency.
- Customization Options: Flexible duct connectors come in various sizes, materials, and temperature resistances to meet specific industry requirements, ensuring optimal performance in unique conditions.
What's the Difference Between a Flexible Air Duct and a Flexible Duct Connector?
It’s easy to confuse flexible air ducts with flexible duct connectors, but they serve distinct purposes:
- Flexible Air Ducts: These direct airflow through the duct system. They are long, flexible tubes often made of insulated materials.
Flexible Duct Connectors: These do not transport air but act as joints between ductwork sections and equipment, isolating vibration and noise. Flexible duct connectors are shorter and constructed to bridge gaps, not to carry airflow.
Understanding this difference is essential for engineers and contractors who need to select the appropriate components for vibration control.
Common Applications of Flexible Duct Connectors
Flexible duct connectors are invaluable in various industries, especially where equipment vibration or noise must be controlled. Some typical applications include:
- HVAC Systems: Used extensively to reduce vibrations and noise from fans, blowers, and other mechanical components.
- Automotive and Aerospace: Applied in systems where ventilation requires flexibility, but vibration control is critical, such as exhaust and HVAC systems.
- Industrial Ventilation: Employed in factories and industrial sites to control noise and vibrations from large equipment, improving working conditions and system longevity.
What Should You Consider When Choosing a Flexible Duct Connector?
When selecting a flexible duct connector, consider the following factors to ensure you meet the demands of your application:
- Size and Fit: Ensure compatibility with the ductwork and equipment specifications.
- Material Compatibility: Choose materials that can withstand the environment's temperature, humidity, and chemical exposure.
- Temperature Resistance: High-heat environments require materials that won’t degrade quickly.
- Durability and Quality: Investing in high-quality connectors reduces long-term costs and improves system reliability, especially for large-scale operations.
These considerations help guarantee the performance and longevity of the duct system.
Conclusion
Flexible duct connectors play a critical role in HVAC, automotive, and industrial systems by isolating noise, reducing system wear, and enhancing energy efficiency. By selecting the right flexible duct connector, professionals in HVAC, construction, and manufacturing industries can improve system performance, protect their investments, and ensure a quieter, more comfortable environment for their facilities.